Elastic waterproofing membrane IMPELAST
Sealing compound Impelast
SEALCOAT-IMPELAST-GREY-20KG

Register now and access more than 125,000 products
Continuous watertight membrane
- Recommended for various surface types: concrete, bitumen sheets, metal, wood and asbestos cement
- Can be used in vertical and horizontal applications
- Adapts to the surface to be coated
- Creates a continuous and watertight protective layer for more secure sealing
Suitable for encapsulating cement-asbestos sheets in accordance with the standard UNI 10686:1998
- Safety: blocks dispersal of asbestos fibres
- Covering of old roofs consisting of both flat and corrugated asbestos sheets
- Suitable for encapsulation types “A”, “B”, “C” and “D”
Water-based single component
- Ready to use
- Easy application
- No waste
Resistant to standing water
Suitable for roofs, gutters and level surfaces, even those with no gradient
Effective and long-lasting protection
- Does not require additional protection
- Also resistant on surfaces in industrial areas and marine areas
- UV resistant
Can only be walked on for inspection and checking**
Encapsulation of type A, B and C cement-asbestos products, as provided for by the Decree of the Italian Ministry of Health dated 20 August 1999, with products and systems for authorised companies registered on the appropriate registers for the sector
** the combined use with non-woven fabric (reinforcement of the entire waterproofed surface) will make it suitable for walking on and tiling
While the technical advice given is based on our experience and should be followed, it is purely indicative and must be confirmed through extensive practical tests. This does not remove the purchaser's responsibility to personally test our products to see whether they are suitable for the planned use
Do NOT apply the products in the following cases: Surface temperatures of less than +5°C, imminent rain, wet surfaces, presence of moisture
In case of application on new cement surfaces, wait until the cement is fully cured. Not completely dried layers of IMPELAST will be damaged by rain, dew and fog. Humidity and low temperatures prolong drying times. On light slabs and on wooden surfaces, complete the waterproofing procedure with non-woven fabric reinforcement. Before carrying out waterproofing, check the internal moisture content of slabs and whether or not moisture vents are required.
Preparation of surfaces
Carry out preliminary cleaning operations for the surfaces in accordance with the methods set out by the regulations in force
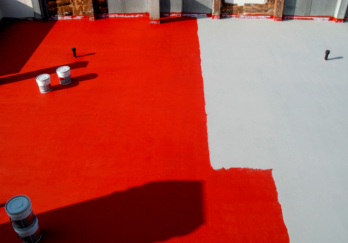
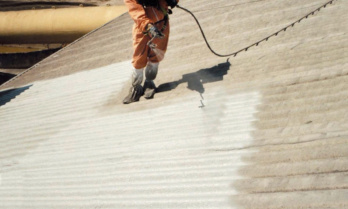
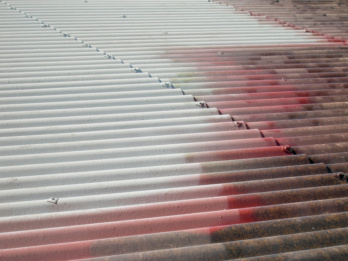
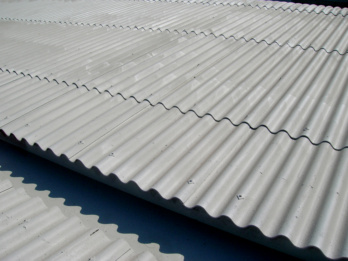
Use with an airless sprayer: | ||
nozzle diameter in inches | fan in cm | pump type (l/min.) |
0,021 | 40 | 8 - 10 |
0,023 | ||
0,031 | 15 - 20 |
Encapsulation of type A, B and C cement-asbestos products, as provided for by the Decree of the Italian Ministry of Health dated 20 August 1999, with products and systems for authorised companies registered on the appropriate registers for the sector
Datasheets(X)
Waterproofing for flat coverings that are not walked on**, flat roofs, old bituminous layers, guttering and sheet-metal roofing. Watertight and flexible layer for micro-cracked surfaces
Preparation of surfaces:
Remove flaking, friable or non-adhering parts, paints, rust, dust and release agents. All surfaces to be treated must be solid, clean and dry. Surfaces with irregularities, very rough plaster and castings, holes, gravel pockets, cracks etc. must be repaired and/or smoothed. Check the soundness and efficiency of water flow points (waste water). Treat or assess in advance any expansion joints: carry out prior sealing of control and insulation joints using the PU 40+ structural adhesive and sealant product. Before sealing, insert backfill material acting as a "third wall" at the bottom of the joint. Where necessary, according to the degree of moisture of the surface, prepare appropriate condensation outlets. Any critical points, or where the product is highly mechanically stressed, should be reinforced with non-woven fabric 130 g/m2 (joints, connections with vertical components etc.) or elastic bands, as needed, inserted between two layers of IMPELAST. The product is normally ready to use. When used as primer, it can be mixed with water, either by hand or with a mechanical mixer at low speed
Cement surfaces:
Treat the surface with primer composed of IMPELAST diluted to 50% with water (2 parts IMPELAST to 1 part water) at 300 g/m2. In the case of pre-stressed concrete or porous materials (e.g. tuff), prepare the surface with B4 primer. In the case of damp and absorbent supports, use BK10 PRIMER at 150–300 g/m2 in accordance with absorption by the surface
Bituminous surfaces:
Flaking bituminous surfaces must first be restored. Self-protected bituminous membranes with slate shavings must be pre-treated with primer composed of IMPELAST diluted to 50% with water at 300 g/m2. On non-self-protecting surfaces, apply B4 primer at approximately 120 ml/m2. Then apply IMPELAST after no less than 4 hours and no more than 24 hours. For white Impelast, use of BK10 PRIMER at approximately 150 g/m² is recommended in order to avoid oil potentially seeping from the recently installed bituminous membranes
Tiled surfaces:
On non-absorbent ceramic surfaces, apply C20 A primer at approximately 250 g/m2. For absorbent surfaces, apply B4 primer at approximately 250 ml/m2 depending on the porosity of the surface
Metal surfaces:
Surfaces affected by rust, after thorough cleaning and repair of damaged parts, must be pre-treated with Rust Converter. Then apply Rust-Stop primer or another suitable primer. On aluminium surfaces, start with light sanding, then clean, degrease and pre-treat with C20 primer, approximately 200 g/m²
Wood surfaces:
Pre-treat wood surfaces with B4 primer, approximately 250 ml/m2. If the wood is painted and in an excellent condition, light sanding and subsequent cleaning is sufficient before applying the primer
After thoroughly preparing the surfaces, apply the first layer of IMPELAST at 1 kg/m2 using a roller, brush or airless sprayer. Wait until fully dry, then apply the second coat, approximately 1 kg/m2. We recommend applying the layers in contrasting colours so to make distributing the product easier
For floors made of pre-stressed reinforced concrete slabs, follow these steps:
- Pre-treat the surface with B4 primer
- Seal the structural joints with PU 40+ structural adhesive and sealant and filler material. (See the "Preparation of surfaces" section)
- Carry out the IMPELAST treatment with non-woven fabric reinforcement
Waterproofing with non-woven fabric reinforcement:
- Adequately prepare the surface (see "Preparation of surfaces" section, then refer to the type of surface to be treated)
- Apply the first coat of IMPELAST at 1 kg/m² undiluted or slightly diluted with water (max. 5%) using a roller, brush or airless sprayer
- Overlap new non-woven fabric by 100 cm, ensuring that it is well impregnated and taking care not to leave bubbles or air pockets. Overlap the different geotextile layers by at least 10 cm
- When dry, apply a second coat of undiluted IMPELAST at 1–1.2 kg/m². Be sure to overlap the waterproofing material by about 10–20 cm with vertical components at the joints
Type A, visible outside (Validation report no. 250697 by the Giordano Institute)
- 1) After cleaning the surfaces, apply a coat of B4 primer at between 200–300 ml/m2
- 2) When dry, apply a first coat of IMPELAST at 400–500 g/m2
- 3) When completely dry, apply a second coat of IMPELAST, which must be in a contrasting colour to the previous coat, at 400–500 g/m2
Type B, visible inside (Validation report no. 258004 by the Giordano Institute)
Type C, not visible, as a support for formwork (Validation report no. 258005 by the Giordano Institute)
- 1) After cleaning the surfaces, apply a coat of IMPELAST diluted with water (ratio 1:1) at between 200–300 g/m2
- 2) When dry (after approximately four hours), apply a first coat of IMPELAST at 400–500 g/m2
- 3) When completely dry, apply a second coat of IMPELAST, which must be in a contrasting colour to the previous coat, at 400–500 g/m2
Type D, for removal procedures (Validation report no. 250700 by the Giordano Institute)
After cleaning the surfaces, apply IMPELAST at 250 g/m2 diluted at 35% with water
Chemical basis | Elastomeric resins in aqueous emulsion |
Moulded density | 1.39 kg/l |
Min. processing temperature | 5 °C |
Max. processing temperature | 35 °C |
Min./max. processing temperature | 5 to 35 °C |
Breaking elongation | 400 % |
Max. cold bending temperature | -20 °C |
Application quantity in weight/area | 1 kg/m² |
Dry residue | 72.7 % |
Tensile strength | 1 N/mm² |
Drying time | 24 h |
Conditions for drying time | at 23°C |
Ultraviolet resistance | Yes |
Select RAL-colour code
!! NOTE: On-screen visualisation of the colour differs from real colour shade!!